In New Zealand, hydrogen steelmaking from ironsand has the potential to eliminate CO2 emissions arising from the manufacture of all steel consumed in the country and in future, emissions globally.
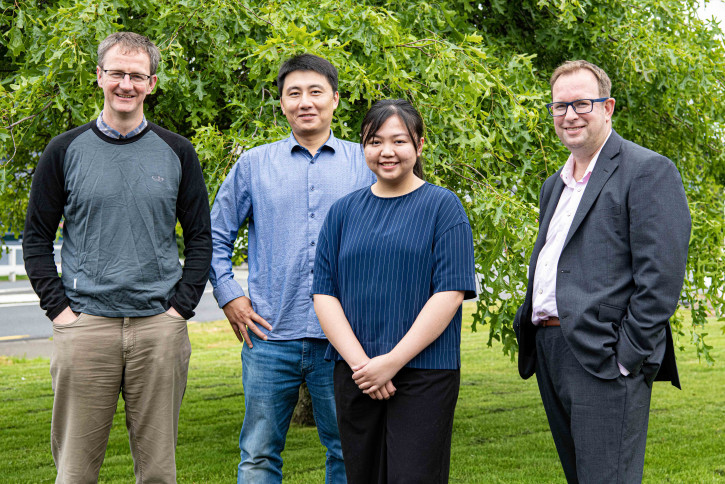
Globally the iron and steel industry is responsible for producing 2.6Gt of CO2, or 7% of the world’s total CO2 emissions. In New Zealand, steel and iron production is the single largest industrial source of CO2 emissions, representing 55% of industrial emissions and around 5% of total gross emissions.
While our knowledge of materials and process control have drastically improved since the Iron Age, the underlying chemistry has stayed largely the same.
Researchers at Victoria University Wellington— Te Herenga Waka and Robinson Research Institute have demonstrated how hydrogen can be used instead of coal during the steelmaking process, potentially eliminating carbon dioxide emissions from New Zealand’s steel industry. Producing iron currently relies on the use of coal to generate a reaction. Coal is used as both the chemical reducing agent and the thermal fuel to heat the reactor, resulting in the emission of large quantities of CO2.
Replacing hydrogen for coal, Dr Chris Bumby and his team have demonstrated the hydrogen-ironmaking reaction in a custom built fluidised-bed reactor, which reacts New Zealand ironsand with hydrogen gas at temperatures up to 1000⁰C, to produce very high-purity iron. As the hydrogen reactor is entirely electrically heated, it could be powered by New Zealand’s renewable electricity, ensuring that the entire process does not emit carbon dioxide.
Features and benefits
Lower carbon emissions
Increased DRI
Hydrogen steelmaking has the potential to substantially increase the direct reduced iron (DRI) process intensity, due to the rapid kinetics of hydrogen compared to carbon.
Next Steps
The production of direct reduced iron (DRI) using hydrogen is a new pre-commercial technology. The research has established an initial proof-of-concept, small-scale fluidised bed reactor with several key advantages over alternative process technologies. The next step is to scale this technology up to pilot scale and beyond.
We are currently seeking potential partners to support the scale up to commercial reality.