Combining the first two steps to make styrene means that it is a lot easier and faster to produce.
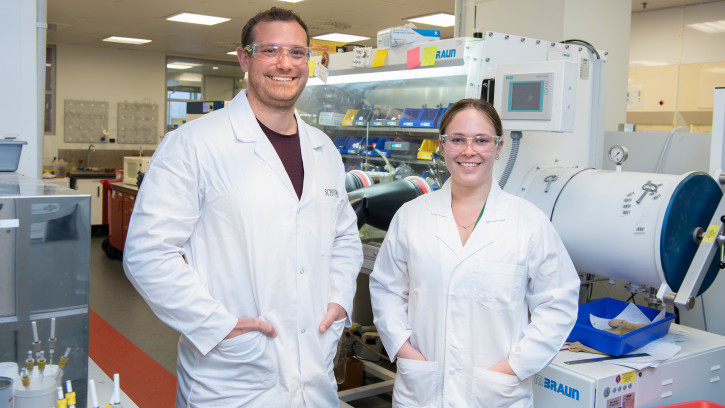
Styrene is a derivative of benzene, a colourless liquid used to make plastics, resins, nylon and synthetic fibres. The way that styrene is made today follows three catalytic steps through the Friedel-Crafts alkylation reaction. However, the first two steps involve using a particularly toxic reagent, which is not only expensive but also produces excessive waste.
Researchers at Te Herenga Waka—Victoria University of Wellington have developed a new cost-effective process, transforming the first two steps of the styrene pathway into a one catalytic reaction. No toxic products need to be used, meaning production is more environmentally friendly than current measures and can be made at a significantly lower cost.
Features and Benefits (easier, faster, greener)
Easier and faster way of producing styrene
Wide variety of uses
Transforming the first two steps into a single catalytic reaction is a vital transformation in both an academic and industrial context, providing access to a wide variety of intermediate compounds, fine chemicals and feedstocks.
More environmentally friendly
This method is by-product free and the starting materials are generally cheaper and more readily available.
Next steps
We are now looking for partners in the industry to take this promising technology forward. There is an opportunity for a licensee or research partnership with a company that is active in petrochemistry.
For further information about partnering with us on this project, contact the Wellington UniVentures staff member below.